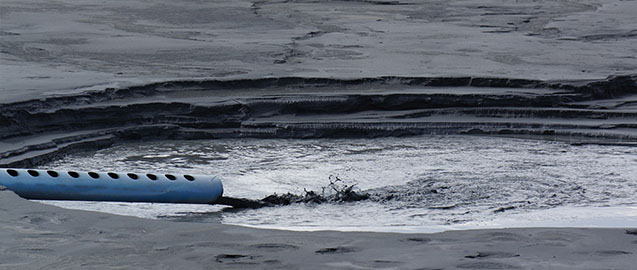
Slurry in a sand magazine.
Photo: Pontus Westrin, SGU.
Enrichment process and tailings
Valuable metals or elements are enriched and separated from the mined ore via ore processing, which also generate a type of waste in the form of tailings. Tailings are often deposited in tailings storage facilities aiming to protect the environment.
As part of the enrichment process, valuable metals or elements are separated in a processing plant via methods that uses physical and chemical differences of minerals where metals are locked. For example, iron is often separated from iron ore via magnetic separation. Enrichment methods used for several other metals, such as copper, lead, zinc, gold and silver, are often flotation, cyanide leaching and gravity enrichment (density differences). In many cases, combinations are used to maximize the enrichment.
Ore processing starts with crushing and grinding. This steps aims to separate mineral grains and expose grains surfaces so that differences in chemical and physical properties of minerals can be used to liberate valuable metals or elements. Crushing and grinding are an important part of the enrichment process, and the one that costs the most in terms of energy to operate.
After the ore is crushed and grinded, the valuable metals need to be separated from what will become tailings. For this, one or more methods are used; the choice of methods depends upon the physical and chemical properties of the ore. In several enrichment plants, gravity enrichment is used, which means that heavier substances (for instance gold) are separated from lighter substances.
At the end of the enrichment process, valuable metals or elements are accumulated at a relatively high concentration and forms what is known as a ‘concentrate’. This concentrate is transported from the processing plant to a smelter, where the concentrations of the metal are further increased by metallurgical processes. The waste generated after the enrichment process, known as tailings, is taken from the processing plant to a storage facility, a tailings impoundment often referred to as storage facility. The tailings often travel through pipelines in what is known as a ‘slurry’, a mixture of tailings and mining drainage water.
The tailings storage facility is designed to store the tailings safely, while protecting the environment. Sometimes the tailings are kept saturated with water; this is primarily to prevent the tailings from being exposed to oxygen, which can cause certain minerals to oxidise. This refers primarily to certain sulphide minerals.
Learn more about sulphide minerals
In the tailings storage facility, there are often built-in sensors and monitoring systems to make sure that the structure is holding up. Because the tailings storage facility often holds large amounts of tailings and water, there is a risk that the structure may break – dam failure – and that tailings and mining drainage water will leak, which can lead to serious consequences to the environment and people. Therefore, stringent requirements are in place on the design and construction of the tailings storage facility.
Mining operators perform self-monitoring of the tailing’s storage facility and supervision is performed by the supervisory authority. Each year, mining operators must submit a dam safety report to the regulatory authority, and every 10 years an overall assessment of the safety of the dam must be carried out.
Svenska kraftnät, the Swedish power grid agency provides guidance on issues related to dam safety in Sweden.
Read more on Svenska kraftnät's website about dam safety (new window)
Last reviewed 2022-06-17