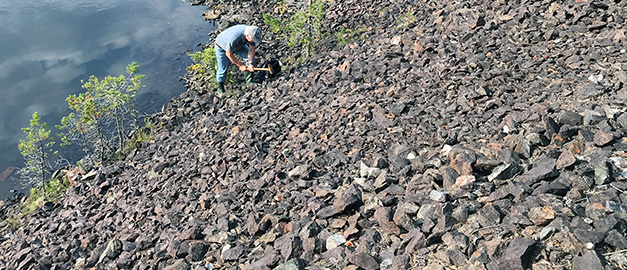
Sampling at Lilla Dambergsgruvan in Bergslagen.
Photo: Helge Reginiussen, SGU
Metals and minerals in mining waste
Old mining waste has the possibility to become new assets. With modern methods, it may be possible to extract minerals and metals from these, something that impossible to extract using older technology. In gangue and tailings there may also be materials that were not financially interesting when the ore was mined, but that are in demand today.
Mining waste or residual material from mining operations and processing is what remains when metals and minerals are extracted from our bedrock. The mining waste consists primarily of gangue, which is the rock that must be removed in order to access the ore and tailings that remain after the ore has been crushed, ground and enriched into a mineral concentrate.
Gangue
Gangue is the rock that is mined to access the ore. Gangue has a small financial value and has usually been placed near the mine or used for roads and ponds in the vicinity of the mine. In earlier times, before various enrichment methods began to be used, the ore was sorted by hand, the hand-picking method. The residual material from picking out by hand can sometimes be rich in metals.
Older gangue landfills
Researchers at Uppsala University have investigated, in a research project, the content of rare and critical metals in old gangue landfills/impoundments in Bergslagen. The landfills/impoundments are remnants of hundreds of mining and mineral processing operations. They have been able to show that there is a large amount of rare metals in the landfills/impoundments, and partly also in which minerals they are present. In several areas, there are metals that are critical for modern and green technology.
Tailings
Tailings is the material that remains after the ore has been crushed, ground and enriched to extract the valuable minerals. The tailings are usually deposited in ponds that are kept covered in water or covered with soil when the facility is shut down or abandoned. At older enrichment plants, the tailings were deposited in the nearest depression or stream.
In practice, it is not possible to extract all the valuable minerals from the ore and still have a financial gain; some will naturally accompany the tailings. To what extent the interesting minerals are unable to be extracted depends upon how valuable they are, or aren’t. When enriching gold ores, 5% or less of the gold follows with the tailings; for sulphide ores with copper, lead and zinc, approx. 10% of the valuable mineral usually stays in the residual material. Iron minerals such as magnetite and hematite are not as valuable and the financial unviability means that tens of percent of the iron mineral become residual material during magnetic sieving and enrichment.
There are quite a number of analyses of metal content in mining waste, however there remains a significant amount of uncertainty about how much there are in total and whether extraction would be financially viable. For rare-earth metals and phosphorus, the potential is considered to be relatively huge. At the present time however, the technical solutions required for the extraction to be profitable do not exist.
It is estimated that the amount of metal in all tailing ponds could replace the ore production in 2013 for three to five years, then the tailings impoundments would be empty.
Phosphorus in tailings
In Swedish iron ore production, large amounts of phosphorus follow. About 40,000 tonnes a year end up in tailings ponds as mining waste. In the mining waste in Kiruna and Malmberget, there is a stockpile of about one million tons of phosphorus.
Phosphorus is an important nutrient for plants and the substance is found in manure that is added to crops. Phosphorus can be recovered from manure and sludge from wastewater treatment plants. The net contribution from these sources corresponds to approximately 25% of the annual supply. Phosphate currently used in manure originates from an imported raw material – apatite.
The iron ores that are mined in Sweden today are apatite iron ores and they contain several percent phosphorus. During the enrichment, a large part of the phosphorus mineral apatite is separated from the ore with the aim of producing a phosphorus-poor iron oxide concentrate, something that today’s blast furnaces require. The phosphor mineral apatite, which also contains rare-earth metals, will follow the tailings.
Extracting this phosphorus and accompanying rare-earth metals in an ecologically and financially sustainable way requires technological innovations. In addition, there is data that suggests that the apatite from apatite iron ores also contains arsenic. Chemical analyses of apatite iron ore from the Grängesberg mine in Bergslagen show a clear correlation between rising levels of phosphorus and rising levels of arsenic.
However most of the phosphorus raw material used globally is raw phosphate from sedimentary rocks, which also contain relatively high levels of cadmium. This has meant that the cadmium content of raw materials has increased in line with increasing food production. Human exposure to cadmium occurs primarily via food and can have negative health effects, such as kidney problems and osteoporosis. Mineral fertilisers with low levels of cadmium may become a future scarce commodity in the world.
Last reviewed 2022-06-17