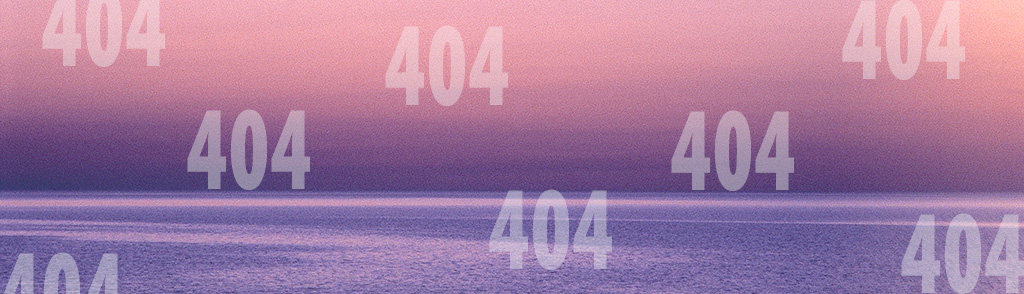
404 - Page not found
Sorry – the page can not be found
You may have followed a broken link, an outdated search result, or there may be an error on our site.
Why did this happen?
Make sure you entered the correct address and try again. If that doesn't help, you can go to the home page or look in the navigation menu if you find the page that way.
Old links?
We sometimes delete pages on the website, which can mean that old links no longer work. Sometimes we also move the pages. In that case, use our search function to find the right one, or navigate using the menu.
Feel free to contact us
If you have ended up here after following a link on our website or if you think something has gone wrong, feel free to send an e-mail to kundservice@sgu.se and tell us. It helps us fix any errors.
Search the siteUse our search function to quickly find the information you are looking for. If you get many hits, you can narrow your search to different parts of the site. |
Last reviewed 2020-10-21